Related Jobs
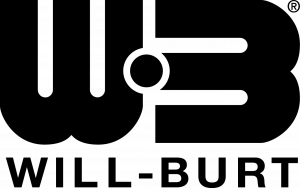
The Will-Burt Company
Job Description
Job Title: Heavy Duty Assembler
Grade: 1
FLSA Status: NE
SUMMARY
Assembles aluminum products, such...
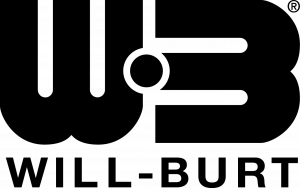
COMPANY OVERVIEW
The Will-Burt Company is the world's premier manufacturer of mobile telescoping masts, towers, trailer systems, and pan and tilt positioners. We offer virtually every mobile payload elevation solution...
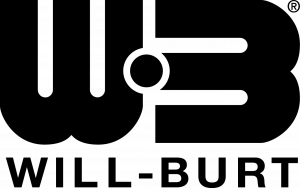
ESSENTIAL DUTIES AND RESPONSIBILITIES include the following.
Employee supervision and control (coaching and training).
Interprets company policies to workers and enforces safety regulations.
Evaluates written...
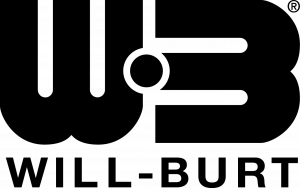
Conducts on the job training.
Attends morning production meetings
Assists with production coordination.
Studies production schedules and estimates worker hour requirements for completion of job assignment.
Rea...
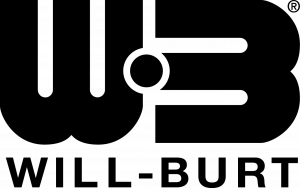
SUMMARY
Loads, unloads, moves, inspects, and receives materials within or near plant, yard, or work site by performing the following duties. Job function will be mainly to serve Will-Burt 312, 515, and occasionally...
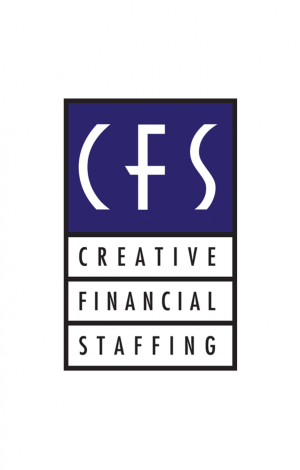
Accounting Manager About our client and the Accounting Manager Opportunity: Our client is a non-profit with an amazing mission. Due to a promotion, they are hiring for a key role in Finance. The growth opp...
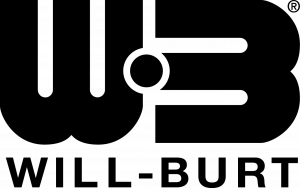
ESSENTIAL DUTIES AND RESPONSIBILITIES include the following. Other duties may be assigned.
Manage development and commercialization of product lines.
Drive delivery of customer solutions through current product...
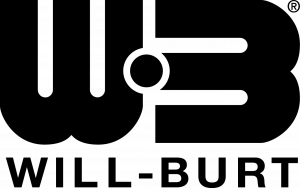
Communicates directly with customers through verbal and written skill using E-mail, customer portals and other similar devices
Transcribes orders to an electronic order entry system
Enters orders and special reque...
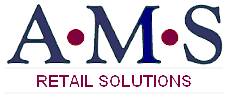
Job Title: Market Manager
Full Time / Hourly
Come work for our Employee Owned Company! Represent a business unit of consumer durables, work with a dynamic team and meet new people every day! Work in a retail envir...
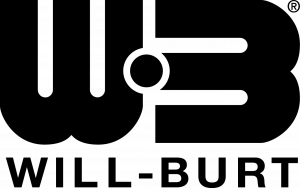
Essential Duties and Responsibilities:
Create, review and submit First Article Inspection documentation to customers as required (PPAP/AS9002).
Participate in Customer on-site Source Inspection activities.
Pro...